In the processing of iron ore, it is crucial to choose the right crushing equipment. For the crushing of large-scale iron ore, a variety of factors need to be considered, such as the hardness of the ore, production requirements, crushing size and so on. The following is a detailed analysis and recommended configuration of iron ore crushing equipment solutions, combining different production requirements and scale to provide multi-angle suggestions:
Key stages of crushing process and equipment selection
Rough crushing stage
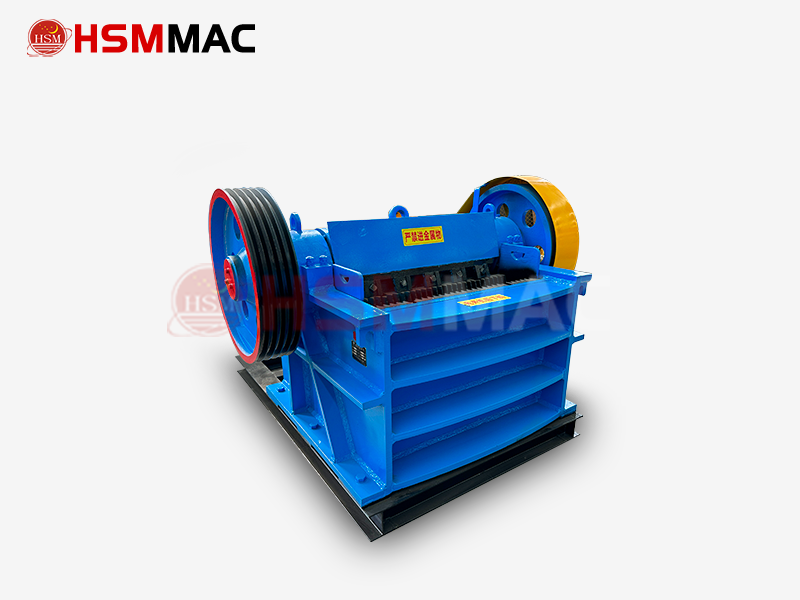
Jaw crusher
Jaw crusher: as the traditional coarse crushing equipment, it is suitable for small and medium-sized mineral processing plant, with simple structure and low maintenance cost, it can crush the raw ore (about 500mm) to 100-300mm.
Middle and fine crushing stage
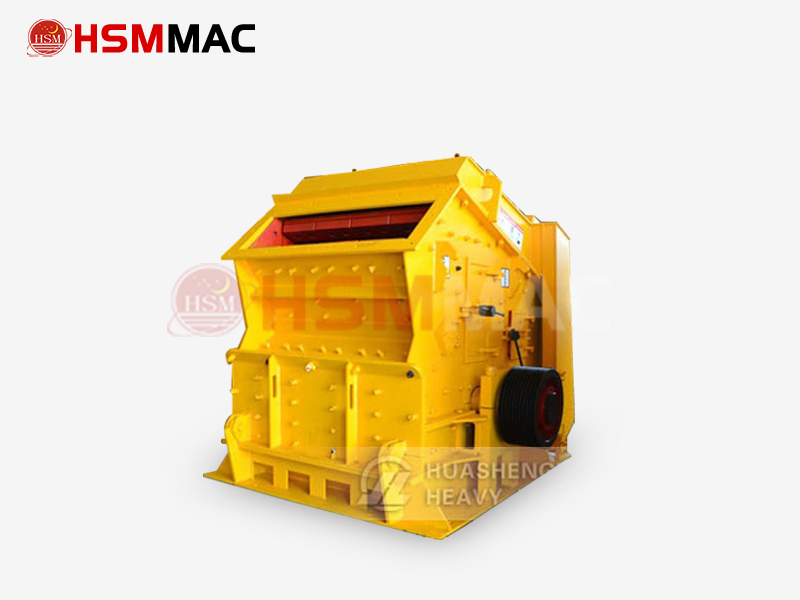
Impact crusher
Impact crusher: suitable for medium and low hardness ores, with large crushing ratio (up to 40) and good particle shape.
Fine crushing stage
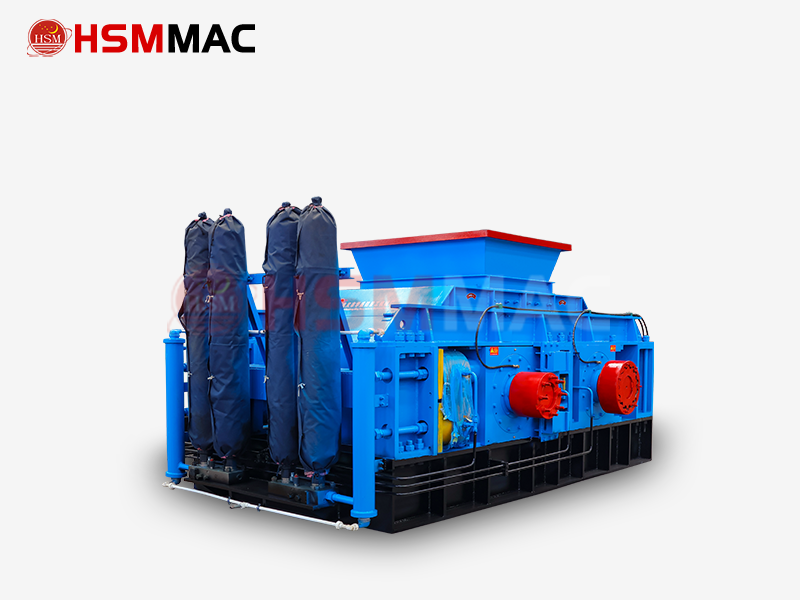
Roller crusher
Roller crusher: suitable for small-scale fine crushing, but the crushing ratio is small, high maintenance cost, less large-scale application.
Screening and dry selection
Vibrating screen: It is used for grading and screening, and the materials after secondary crushing are divided into three levels (e.g. <10mm, 10-40mm, >40mm), which can be dry-selected or returned to crushing respectively, so as to enhance the utilisation rate of resources.
Dry separator: It is recommended to carry out dry separation after fine crushing (e.g. <10mm) to avoid waste of resources due to premature dry separation.
Programme Notes
Large-scale equipment has high initial cost, but lower long-term operating cost; small-scale equipment is suitable for short-term demand, but need to bear higher risk of resource waste.