Asphalt crushing lines, especially systems with integrated crushing and screening solutions. This integrated solution is designed to reprocess waste asphalt pavement material (e.g. milled down old asphalt) into new material that can be reused. Through the crushing and screening processes, these waste materials can be converted into specification-compliant aggregates that can be used in new road laying or repair work. This not only helps to reduce reliance on natural resources, but also significantly reduces project costs and environmental impact.
Asphalt can be recycled at a reuse rate of more than 90 per cent, reducing the need for new aggregate extraction. The replacement rate of recycled material is 30%-50%, reducing road maintenance costs by 20%-40%. Asphalt crushing plant is an important part of asphalt recycling, and its programme design needs to take into account the crushing efficiency, material grade protection, environmental performance and maintenance costs.
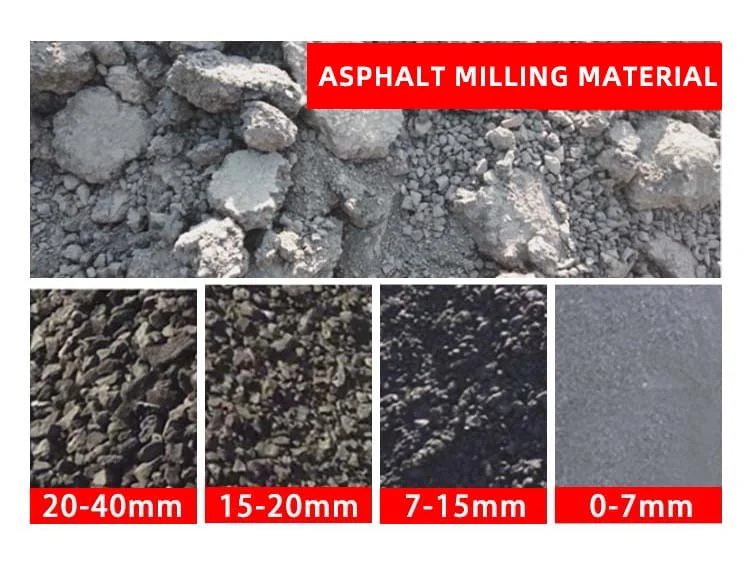
Asphalt crushing effect
Production Line Configuration
Feed → primary crushing → screening (vibrating screen) → secondary crushing → recycling mixing (new asphalt + additives) → product output
Asphalt crushing core equipment types and technical characteristics
1.Double roll crusher
Working Principle: Shear and knead crushing through the teeth of two rolls rotating relative to each other to reduce the damage to the aggregate gradation.
>Advantage: Highly efficient treatment of viscous asphalt milling material, even material output (particle size ≤ 35mm), low energy consumption and low maintenance costs.
Applicable scenario: preliminary crushing of large slabs of asphalt (e.g. materials with lumps up to 150mm after stacking).
2. Roll Crusher (Roll Press Type)
Structure: Adopting parallel rollers rotating in opposite direction, covered with wear-resistant teeth, and controlling the size of discharged material (e.g. 0.5-50mm) through gap adjustment.
Technical highlights: Speed difference design enhances the shearing effect to prevent asphalt sticking.
Flexible crushing technology of double tooth roll crusher
The double-tooth roll crusher adopts kneading type crushing, which reduces the aggregate crushing rate compared with the traditional hammer crushing .
Suggestions for equipment selection
1. Capacity matching: choose the equipment according to the project demand (e.g. 50-100t/h equipment for small projects, 200t/h or more capacity for large projects).
2. Modular design: give priority to mobile or fast assembly equipment, easy to deploy on site.
3. Wear-resistant and maintenance: key components (rollers, screens) need to be coated with high manganese steel or tungsten carbide to prolong service life.
4. Environmental compliance: Ensure that the equipment is equipped with noise reduction (≤75dB) and dust removal systems to comply with environmental construction standards.