The discharge size of roll crusher is mainly controlled by mechanical adjusting device, and its range and uniformity are affected by equipment design, operating parameters and material characteristics.
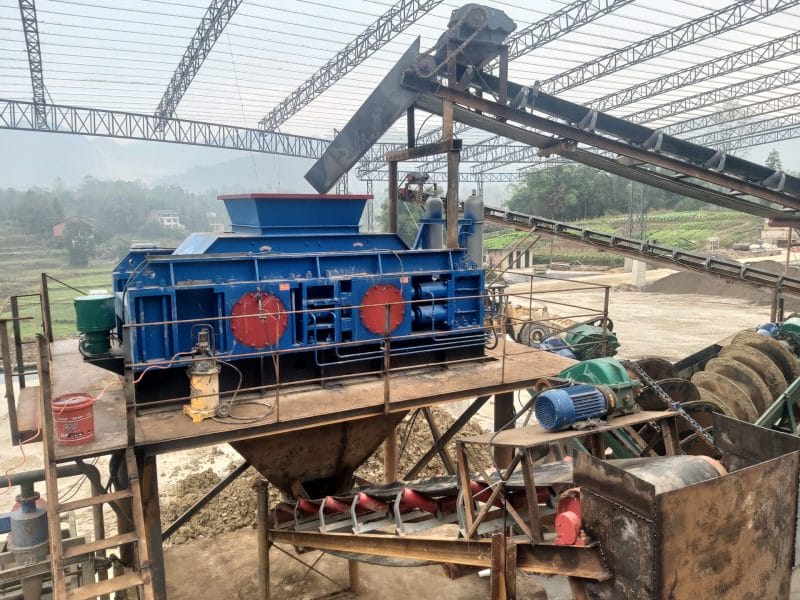
roll crusher
Adjustment Mechanism of Roll Crusher Discharge Size
Wedge adjustment
The position of the wedge is changed by adjusting the bolt: when the wedge is pulled upwards. The gap between the movable roller and the fixed roller increases. And the discharge size becomes larger; when the wedge is pressed downwards. The spring is compressed so that the gap decreases, and the discharge size becomes smaller. Gasket adjustment
Increasing or decreasing the number or thickness of shims can change the gap between the rollers: When the shims are increased, the gap becomes larger and the discharge size increases; when the shims are decreased, the gap is reduced and the size is finer.
Typical range of discharge size
Depending on the model, the size of the roll crusher discharge is usually adjusted between 0.5 and 30 mm.
Example:
Small plants (e.g. 2PG400 x 250): discharge size 2-8 mm, suitable for fine crushing;
Medium-sized equipment (e.g. 2PG610×400): discharging granularity 0.5-30 mm, taking into account the needs of coarse and fine crushing;
Large-sized equipment (e.g. 2PGG1200×800): the discharge size can be as low as 4 mm, suitable for high output scenarios.
Key Factors Affecting Discharge Size
Equipment parameters
Roller diameter and length: the larger the roller diameter and the longer the roller length, the higher the processing capacity, but the particle size may fluctuate due to differences in material distribution;
Motor power: high power equipment can maintain stable crushing force and reduce particle size deviation due to material hardness variation.
Operating conditions
Feed uniformity: Uneven feed can lead to localised overloading or gap variations, affecting particle size consistency;
Material characteristics: hardness, humidity and initial particle size can affect crushing results. For example, high humidity tends to stick to the roll surface, resulting in uneven particle size.
Maintenance condition
Wear of roll surface: Wear of roll surface after long-term use will increase the actual gap, resulting in too fine discharged material, requiring regular maintenance or replacement of rollers.
Optimisation measures for particle size uniformity
Pre-treatment of materials: remove impurities and large materials through screening to reduce the load fluctuations of the equipment; hydraulic or spring protection: automatically yield to the rollers in the event of non-crushable materials to avoid sudden changes in the gap affecting the particle size; dynamic monitoring and adjustment: combined with sensors to monitor the crushing state in real time, and timely adjustment of the gap or feed rate.
Application Scenarios and Suggestions for Particle Size Selection
Coarse crushing requirements (such as building materials, metallurgy): you can choose a model with a discharge size of 10-30 mm, such as 2PG750 × 500;
Fine crushing requirements (e.g. chemical industry, sand making): recommended particle size 0.5-5 mm models, such as 2PG900 × 500;
High uniformity requirements (such as feed processing): need to be combined with roll gap fine-tuning (such as 0.2 mm), can significantly improve the consistency of particle size.
The particle size of the roll crusher is highly adjustable, but it needs to be combined with equipment selection, operation specification and maintenance management to achieve the best results. In practice, it is recommended to refer to the technical parameters of specific models and make targeted adjustments according to material characteristics.