Boulder Rock Crushing sand making programme needs to be combined with raw material hardness (Mohs hardness 7-8), production scale, finished product requirements and site conditions, equipment selection should focus on the examination of wear-resistant parts life and intelligent control system for comprehensive configuration.
Selection of core equipment for boulder rock crushing and sand making
Boulder Rock crushing and sand making Process design
Flow: Jaw crusher (coarse crushing) → Cone crusher (medium and fine crushing) → Roll crusher (shaping sand) → Vibrating screen (grading) → Sand washing machine (purification).
Characteristics: Excellent granularity of finished products, suitable for the production of high grade concrete aggregates for construction.
Supporting equipment and environmental protection measures
Coarse crushing equipment: Jaw Crusher
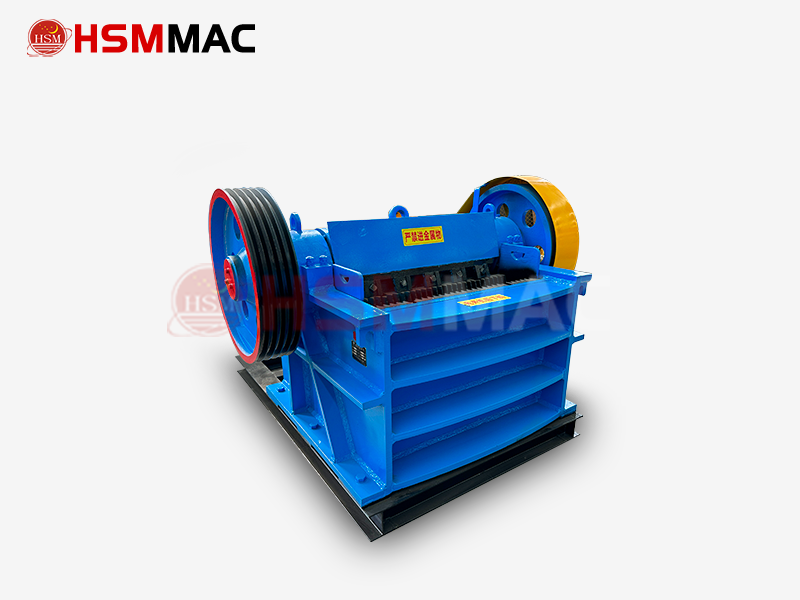
Jaw Crusher
Function: Crushing large river stone (≤500mm) to medium size of 80-150mm, preparing for subsequent crushing.
Technical advantages: deep V-shaped crushing chamber design to enhance the bite capacity, hydraulic overload protection system can cope with the impact of foreign objects.
Medium and fine crushing equipment: Cone Crusher
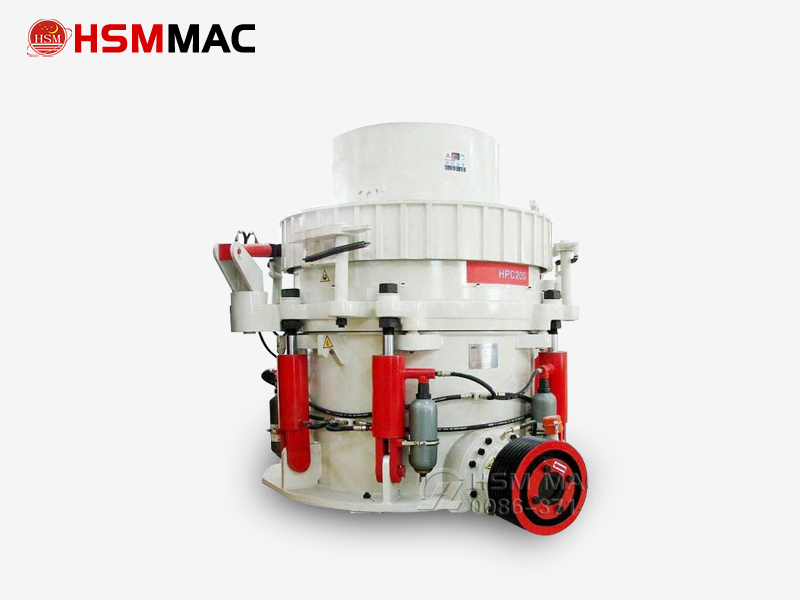
Cone Crusher
Function: further fine crushing of coarse crushed materials to 5-30mm, optimising the particle size and improving the compression resistance.
Technical breakthroughs: laminated crushing principle to reduce needle flake particles, hydraulic adjustment of the discharge opening precision error <±3mm.
Sand Making Equipment: Roll Crusher
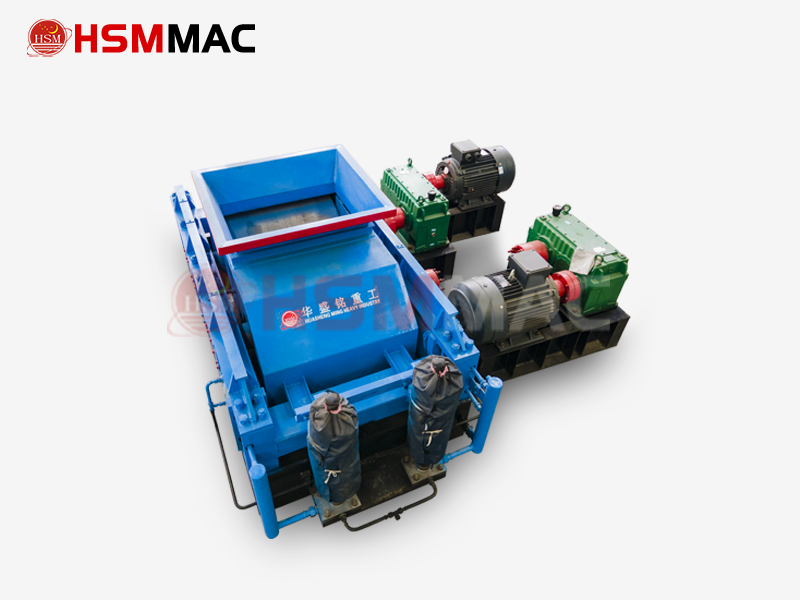
Roll Crusher
Function: Shaping of finely crushed materials to produce 0-5mm graded sand.
Core value: Roll crusher adopts manganese chromium alloy, tungsten carbide and other high-hardness materials, which extends the service life by 2-3 times compared with ordinary steel rolls and reduces the replacement frequency. Modular design simplifies the maintenance process and reduces annual maintenance cost by 40%.
Auxiliary equipment
Feeding system: vibrating feeder (uniform feeding). Screening system: multi-layer circular vibrating screen (grading accuracy ≥98%). Conveying system: wear-resistant belt conveyor (connecting the whole process).
Environmental protection configuration
Dedusting: pulse bag filter (filtration area 2000m2) + water film desulphurisation tower (denitrification rate >90%). Noise reduction: acoustic muffler (noise ≤ 85dB). Wastewater treatment: circulating water sand washing system (wastewater discharge reaches the first class standard).