Volcanic stone with high Mohs hardness and high silica content. In the actual processing belongs to the more difficult to crush, or crushing higher consumption of rock. Therefore, the volcanic rock crushing equipment program should be designed reasonably, crushing project investment at the same time, to consider the operating costs of the production line.
Volcanic stone crushing equipment program design needs to take into account the high hardness of volcanic rock, high silica content, easy to wear and tear of equipment and other characteristics, combined with different production requirements (such as output, finished product particle size, site conditions, etc.), the following is a combination of a number of sources of recommended programs and equipment selection analysis:
Volcanic Stone Crushing process program
Rough crushing + fine crushing + shaping:
Jaw crusher (rough crushing) → Impact crusher (fine crushing) → Roll crusher (shaping).
Advantage: Roll crusher can optimize the particle shape (cubic and angular) and improve the added value of aggregates (e.g. sand and gravel for construction).
Applicable scenarios: projects with high requirements on the shape of the finished product (e.g. concrete aggregate) or the production of mechanism sand.
Key crushing equipment selection and technical points
Jaw crusher (coarse crushing)
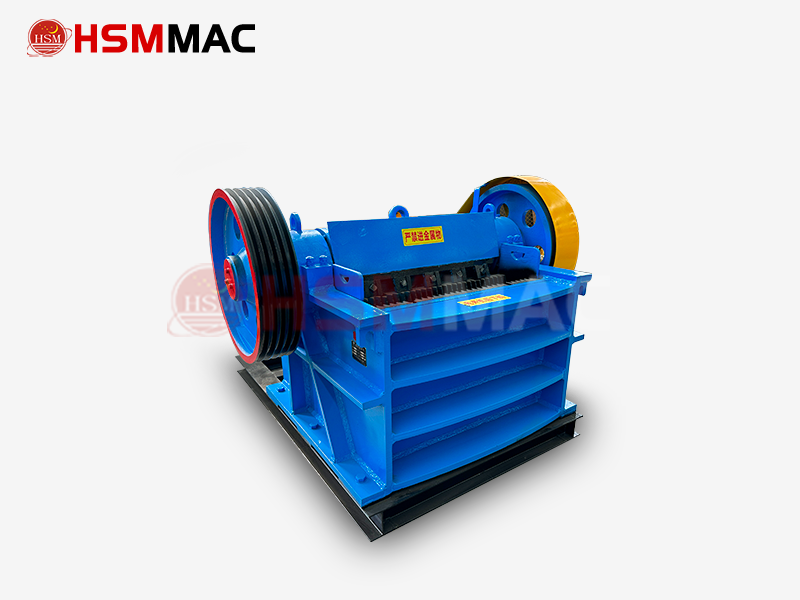
Jaw crusher
Function: Handle large volcanic rock (feed size ≤1300mm), large crushing ratio.
Technical features: deep V-shaped crushing cavity to prevent clogging, high manganese steel jaw wear-resistant.
Impact Crusher (Medium Crushing)
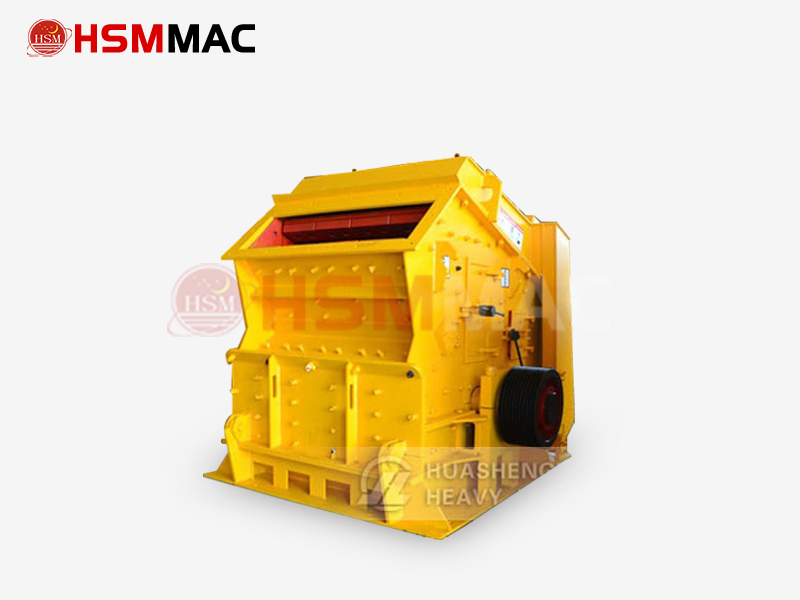
Impact Crusher
Function: Optimize material grain size, suitable for medium crushing of volcanic stone.
Technical features: uniform grain shape of finished products, lower energy consumption.
Roll crusher (fine crushing and shaping)
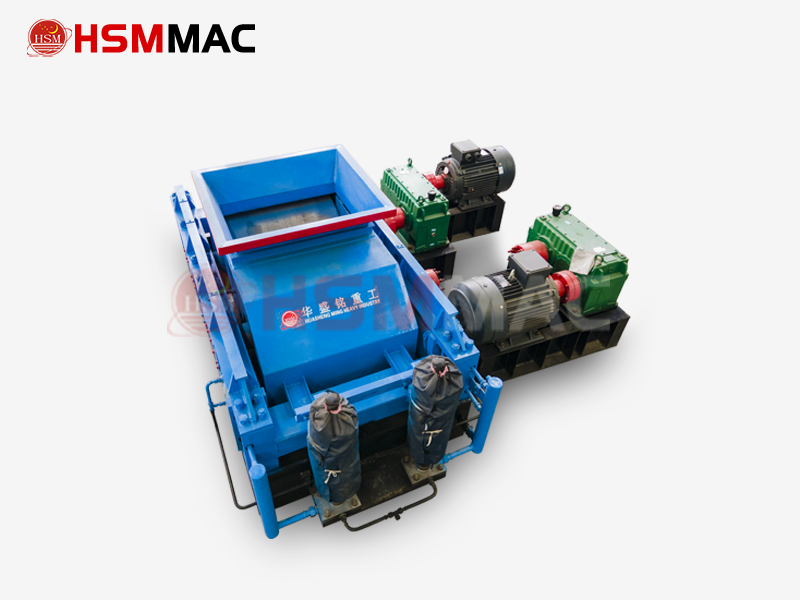
Roll crusher
Function: Precise control of particle size (e.g. 1-5mm) through double-roll extrusion and hydraulic system to meet the demand for high precision.
Technical features: Combined throwing head reduces maintenance cost.
Auxiliary equipment
Screening equipment: rolling screen or vibrating screen.
Feeding and conveying: Vertical screw feeder to reduce screen wear, belt conveyor for closed-loop control of return material.
Dedusting system: low dust design, in line with environmental requirements.