The aluminum slag crushing plant programme needs to consider the crushing efficiency. Metal recovery rate, energy consumption and environmental protection requirements. The following is a summary of the technical solutions after integrating the information from various sources:
Aluminium dross crushing core equipment
Jaw Crusher + Four Roll Crusher + Eddy Current Sorting + Intelligent Dust Removal System
Crushing equipment selection key points
Coarse crushing equipment
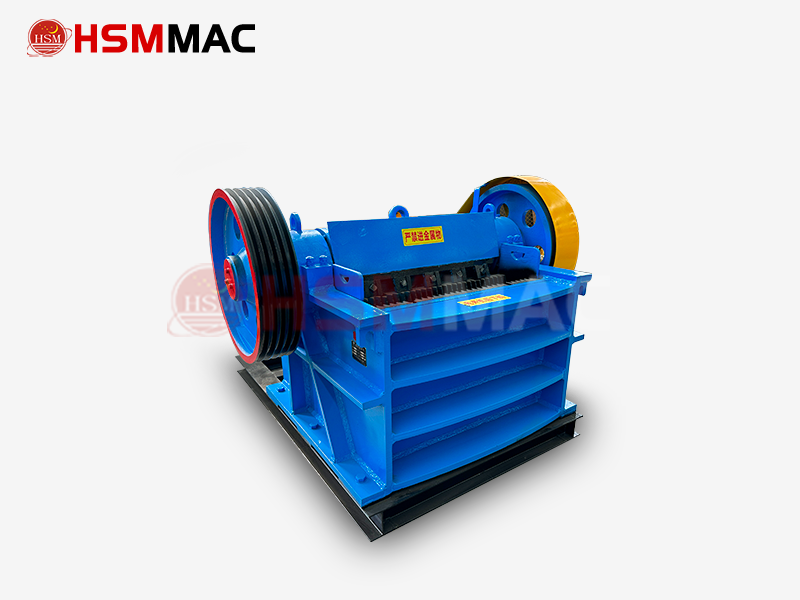
Jaw crusher
Jaw crusher: Large processing capacity, capable of crushing large steel slag over 300mm, matching with secondary crushing.
Fine crushing equipment
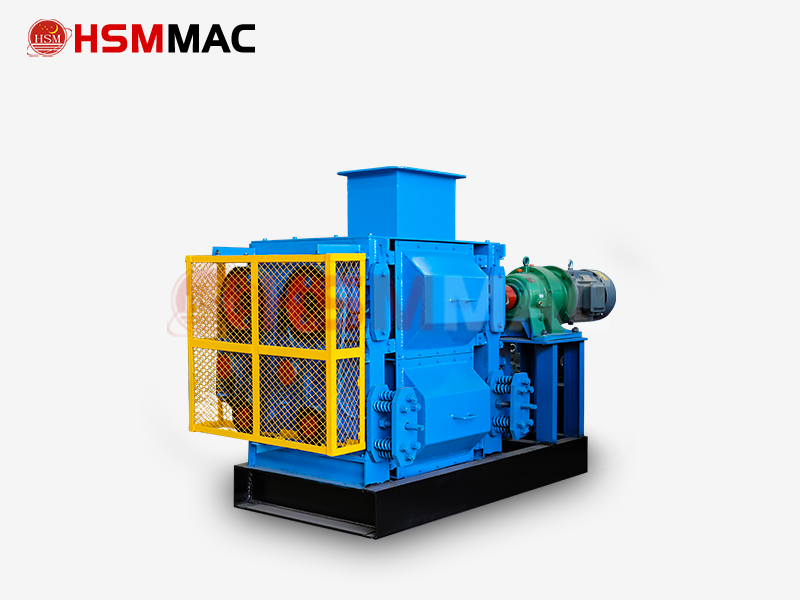
Four Roll Crusher
Four Roll Crusher
Technical features: Crushing is achieved through four-roll extrusion, shearing and grinding, and the gap between the upper and lower rolls can be adjusted to control the particle size of the discharged material.
Advantage: Both coarse and fine crushing function, suitable for aluminium dross with more iron impurities (such as aluminium ash dross), easy to separate by magnetic separation after crushing.
Advantages of steel slag crushing programme
Through three-stage crushing + four magnetic separation (suspended magnetic, cylinder magnetic separator, etc.), large slag steel (TFe>80%), particle steel (TFe 60-85%), fine powder (TFe 30-60%) can be recovered. The metal iron content of tailing slag is ≤1%, which meets the standard of building material aggregate (e.g. concrete aggregate needs to be ≤5mm).
Energy saving and environmental protection
Adopt ‘more crushing and less grinding’ process to reduce the energy consumption of grinding (steel slag Bond Index 20-30kW-h/t). Equipped with pulse dust collector (dust concentration ≤20mg/m³) and soundproof cover, in line with environmental emission standards.