Calcite has low hardness (Moh’s hardness 3) and is friable, preference is given to extruded crushing equipment (e.g. impact breakers, roller sand makers) to reduce over-crushing.
Calcite crushing sand making basic process:
Raw ore → Vibrating feeder → Jaw crusher (coarse crushing) → Impact crusher (medium crushing) → Roller sand making machine (fine crushing and shaping) → Vibrating screen classification → Sand washing machine (optional) → Finished product storage.
Core crushing equipment selection
1.Jaw Crusher
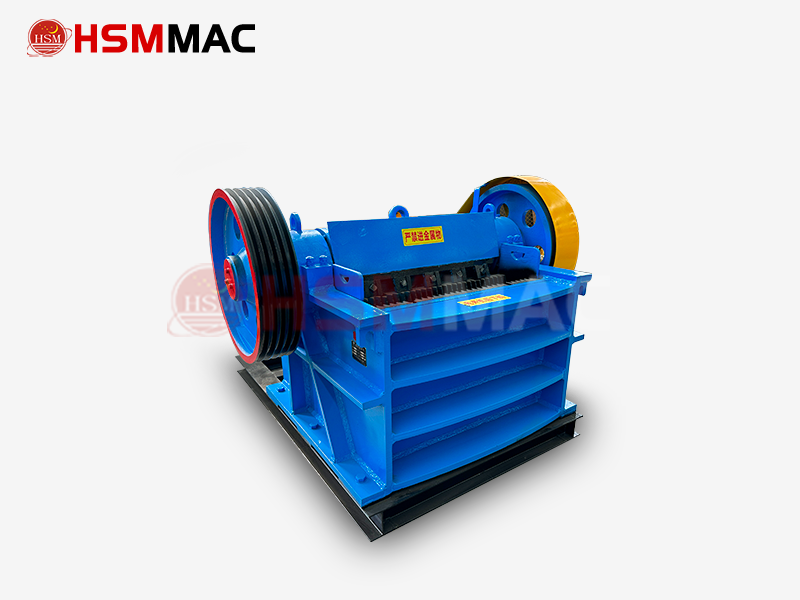
Jaw Crusher
Applicable stage: primary crushing (coarse crushing)
Advantage: large crushing ratio (up to 6-8), simple structure, low maintenance cost, suitable for processing large calcite (feed size ≤ 1200mm).
Recommended scenario: the first process of all scale production lines, especially suitable for high hardness or large ores.
2.Impact Crusher
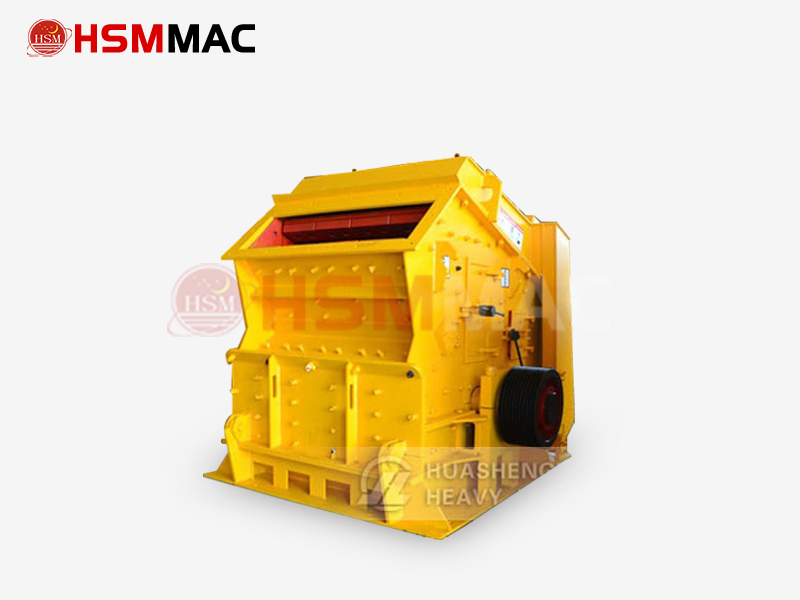
Impact Crusher
Applicable stage: medium and fine crushing
Advantage: high crushing efficiency, good grain shape (≥85% cubic), suitable for medium hardness calcite, processing capacity up to 50-500 tonnes/hour.
Special design: equipped with wear-resistant hammers (such as Mn18Cr2 material), the service life can reach more than 6000 hours.
3.Roller sand making machine
Applicable stage: medium-fine crushing to ultra-fine crushing
Advantage: precisely controllable particle size (stepless speed regulation), low energy consumption, low noise, in line with the requirements of green production.
Optimisation: Match with hydraulic system to achieve ±2mm precision of discharge size.
Notes on crushing and sand making process
1. Equipment maintenance: regular inspection of wearing parts (such as hammerheads, rollers), the use of wear-resistant alloy material to extend the life.
2. Environmental compliance: equipped with pulse dust collector and closed conveyor belt to reduce dust spillage.
3. Automation upgrading: introducing intelligent monitoring system (such as PLC control), adjusting crushing parameters in real time to improve efficiency.
This calcite crushing and sand making solution is suitable for projects with high requirements for environmental protection and the need to flexibly adjust the fineness of sand and gravel (e.g. high-end building materials)