Bentonite is a montmorillonite-based water-bearing clay mine, hardness 1 to 2, density 2 to 3g/cm, belongs to the softer texture of the non-metallic minerals, also known as porphyry, soapstone or bentonite. According to the nature of bentonite, bentonite applicable crushing equipment are: jaw crusher, roller crusher.
Bentonite crushing process
Jaw crusher → impact crusher → roll crusher → vibrating screen → conveying system
Rough crushing stage equipment selection: jaw crusher
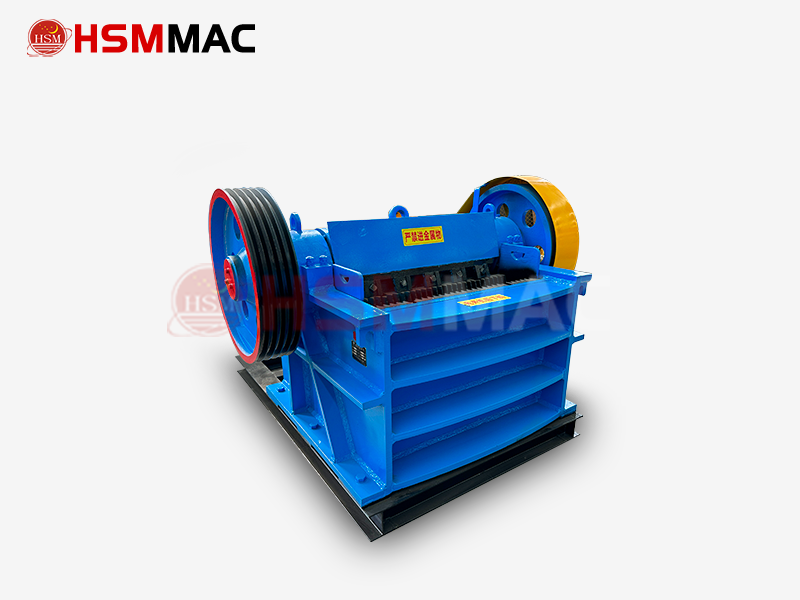
jaw crusher
Applicable scenario: preliminary crushing of raw bentonite ore (feed size ≤ 720mm).
Advantages: simple structure, low maintenance cost, deep crushing cavity and no dead zone, stable processing capacity, better dust control.
Recommended models: such as PE750 × 1060 jaw crusher (200 tonnes per hour production line commonly used).
Medium and fine crushing stage equipment selection: hydraulic roller crusher
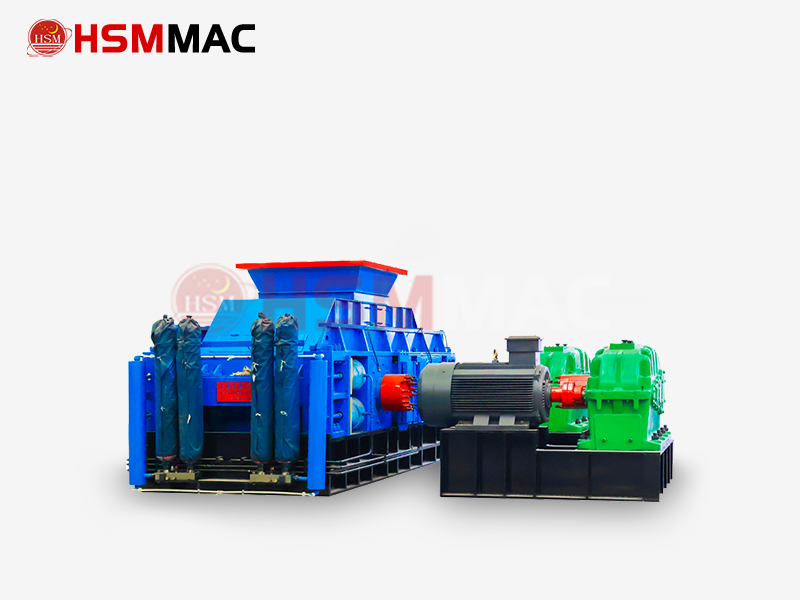
hydraulic roller crusher
Applicable scenarios: Requirements for precise granularity of discharged materials (e.g. sand making or fine crushing to 0-5mm).
Advantages: adjustable roll spacing, full hydraulic system balance flashback protection, long roll skin life, low maintenance costs.
Recommended model: large hydraulic roller machine such as 2PGY1500×1000 (150-200 tonnes per hour).
Auxiliary equipment and supporting programmes
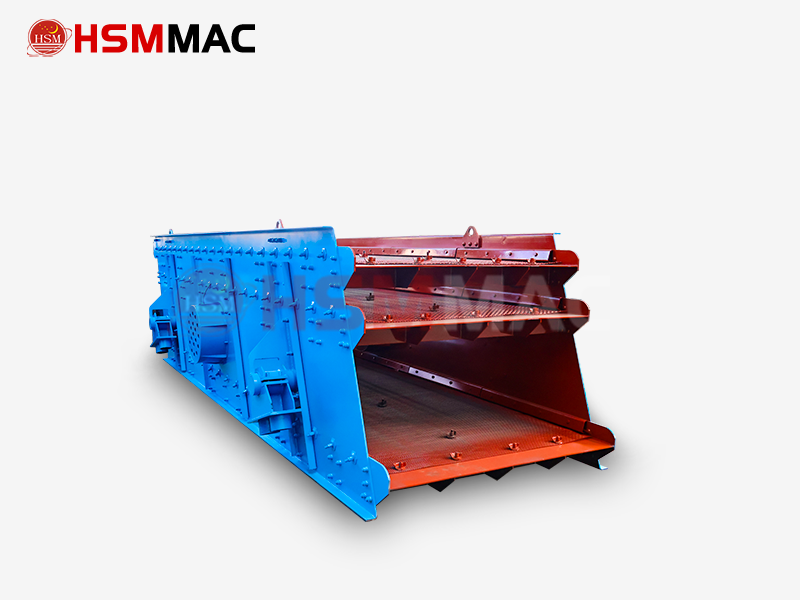
Vibrating screen
1. Screening equipment
Vibrating screen: It is used to classify the materials after crushing, such as S5X vibrating screen which can classify the finished products of 0-5mm, 5-10mm and so on.
2.Automatic control system
Advantage: By automatically monitoring and adjusting the crushing parameters (e.g. bottom flow pump speed, flocculant addition), it can improve the efficiency and reduce the energy consumption.