The design of copper ore crushing programme needs to take into account the ore hardness, particle size requirements, capacity demand and investment budget. Reasonable equipment selection and process flow can significantly improve crushing efficiency, reduce energy consumption and operating costs. The following are the key configuration and selection suggestions.
Copper Ore Characteristics and Crushing Difficulties
Copper ore (e.g. cuprite) is usually of medium hardness (Mohs hardness 3-5), but it may contain impurities such as clay and silica, which can easily lead to adhesion or clogging. Therefore, the crushing equipment needs to have strong adaptability and wear resistance.
Copper ore crushing usually adopts three closed-circuit crushing process, the specific flow is as follows:
Rough crushing stage
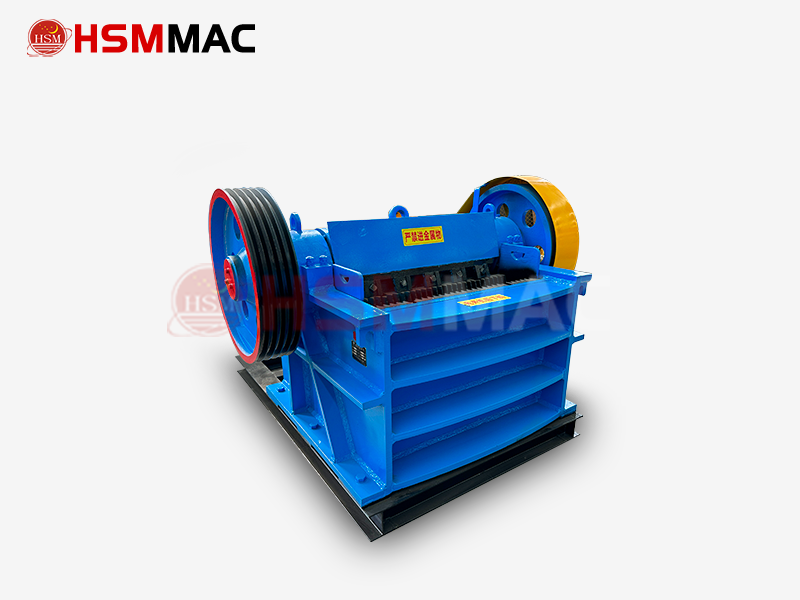
Jaw Crusher
Equipment: Jaw Crusher
Function: Processing large raw ore (feed size ≤1500mm), crushing to ≤300mm.
Advantages: simple structure, large capacity, strong adaptability, especially suitable for high wet ore.
Medium and fine crushing stage
Equipment: Impact crusher
Function: further crush the roughly crushed material to ≤50mm, and form a closed-circuit cycle through vibrating screen.
Advantage: Cone crusher adjusts the discharge opening hydraulically to control the uniform particle size; Impact crusher is suitable for fine crushing and shaping to reduce over-crushing.
Ultra-fine crushing and grinding
Equipment: High pressure roller mill
Function: Grinding the ore after fine crushing to ≤0.5mm, providing suitable particle size for subsequent flotation.
Process optimisation
Copper ore adopts the strategy of ‘more crushing and less grinding’ to reduce the grinding load and energy consumption. Closed-circuit screening design can improve crushing efficiency and avoid over-crushing.