Quartz crushing and sand making equipment programme needs to be designed according to the characteristics of raw materials. The requirements of the finished product (particle size, purity) and production scale. The following is a comprehensive programme of multiple industry equipment configuration recommendations:
Mainstream Configuration Programme
Classic high-efficiency combination: Jaw Crusher + Impact Crusher + Roller Sand Making Machine + Sand Washer
Core equipment configuration
Rough crushing stage
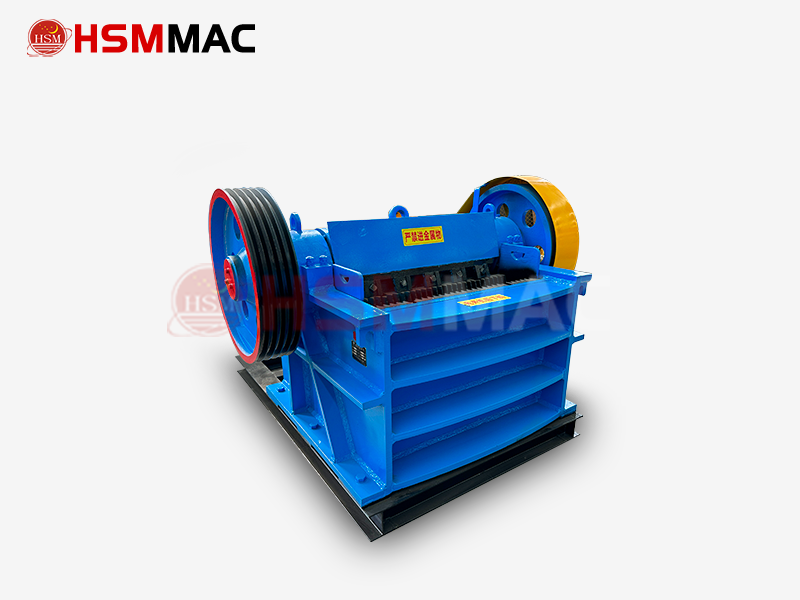
Jaw crusher
Jaw crusher: used for preliminary crushing of large quartz stone (feed size ≤1200mm, discharge ≤300mm), with high crushing ratio and impact resistance.
Middle and fine crushing stage
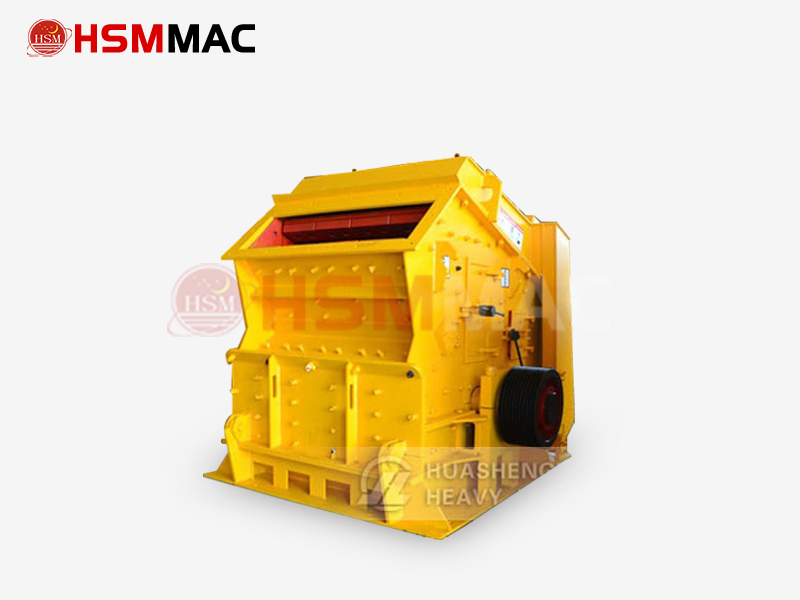
Impact crusher
Impact crusher: used for fine crushing of sand and gravel, with high crushing efficiency, suitable for small and medium-sized production lines.
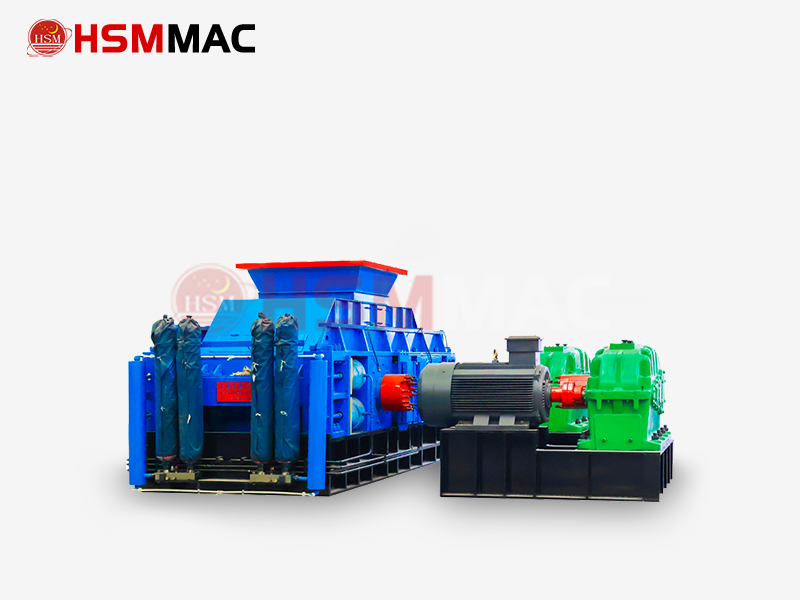
Roller sand making machine
Roller sand making machine: core equipment, both crushing and shaping functions, good grain shape of finished sand (≥80% cubic), energy consumption is 50% lower than traditional equipment.
Screening and washing
Multi-layer circular vibrating screen: grading and screening (screen mesh 5-50mm adjustable), separating qualified particle size materials.
Bucket wheel sand washer: removing surface clay and dust, reducing Fe₂O₃ content (from 0.1% to 0.05%).
Quartz crushing and sand making equipment programme
Process Flow Design
Quartz dry sand process
Flow: Jaw Crusher rough crushing →Impact crusher medium crushing → vibrating screen → sand making machine shaping → finished sand.
>Characteristics: no need to use water, dust removal by bag (emission concentration <5mg/m³), suitable for water-scarce areas, low iron content in the finished product.
Quartz wet sand process
Process: Jaw Crusher rough crushing → Impact crusher → sand washing machine pre-washing → sand making machine shaping → secondary sand washing → dehydration and drying.
>Characteristics: high cleanliness of sand particles, can produce 20-120 mesh wet sand, followed by acid washing, flotation processing for photovoltaic/semiconductor grade sand.
Points for selecting quartz crushing and sand making equipment
Raw material suitability: high hardness quartzite (Moh’s 7) need to choose high-strength cone crusher or impact crusher. The mud content > 5% need to strengthen the washing. If the raw material has high iron content, it needs to be equipped with magnetic separation + acid leaching joint purification equipment.
Finished product requirements
Sand for construction: it should comply with GB/T 14685 standard, and simple screening and sand making can be configured.
Sand for photovoltaic/semiconductor: precision classification (air classifier) and surface passivation treatment (fluidised bed reactor) are required.