The steel slag crushing plant programme needs to consider the crushing efficiency, metal recovery rate, energy consumption and environmental protection requirements. The following is a summary of the technical solutions after integrating the information from various sources:
Process Flow Design
Tertiary crushing + Screening process
Rough crushing stage: Jaw crusher (e.g. PE series) is used to deal with large steel slag (≤300mm), and the discharge size is controlled at 150-300mm.
Medium crushing stage: Impact crusher for secondary crushing, discharge size ≤ 50mm.
Fine crushing stage: Roll crusher crushes the material to ≤5mm, realising efficient dissociation of slag and iron.
Screening and Magnetic Separation: Vibrating screen with three levels of screening (coarse, medium and fine). Combined with permanent magnetic drum and cartridge magnetic separator to recover metallic iron and reduce. The metal content in the tailings to less than 1%.
Core equipment configuration
Jaw crusher × 2 (coarse crushing) Cone crusher × 1 (medium crushing) Roll crusher × 1 (fine crushing) Vibrating screen × 3 (screening) High-efficiency dust collector × 1 (dust control)
Crushing equipment selection key points
Coarse crushing equipment
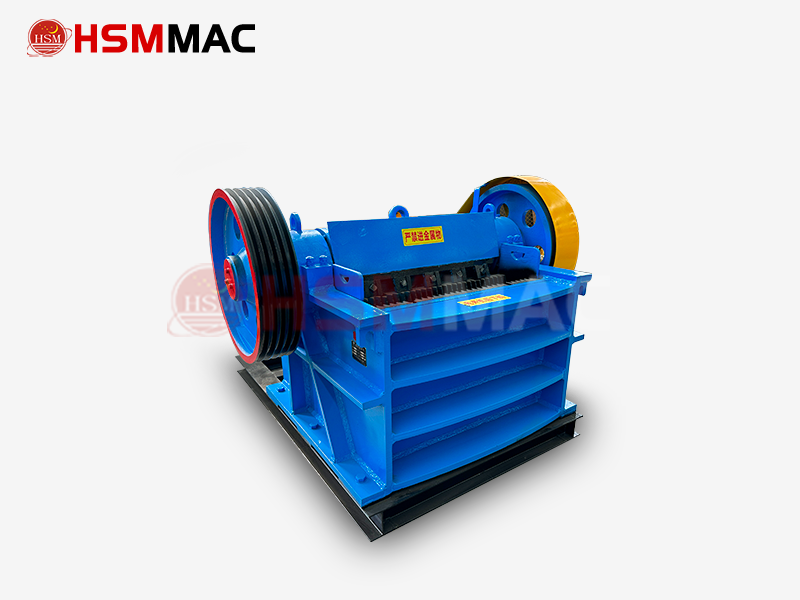
Jaw crusher
Jaw crusher: Large processing capacity, capable of crushing large steel slag over 300mm, matching with secondary crushing.
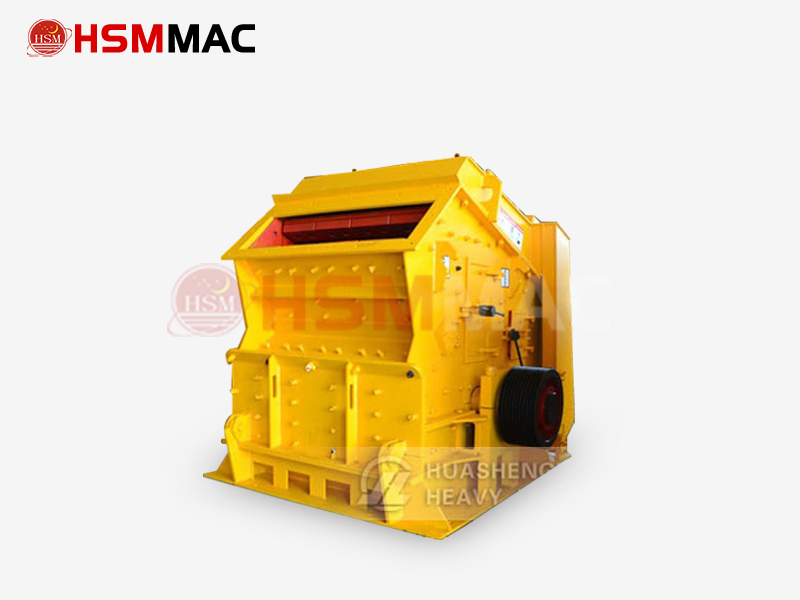
Impact crusher
Impact crusher: adjustable fineness of discharged material (≤50mm), suitable for aggregate production, but sensitive to iron content.
Fine crushing equipment
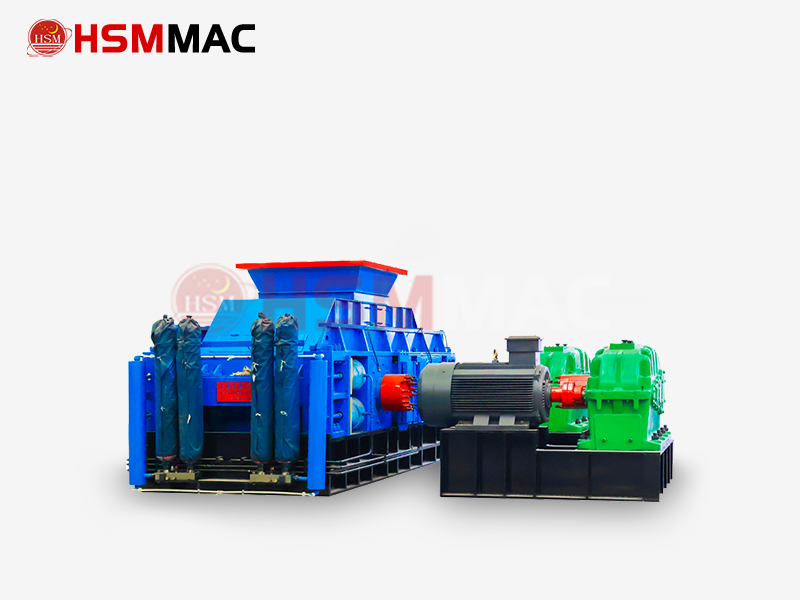
Roll crusher
Roll crusher: metal iron recovery rate increased to more than 95%, can achieve efficient dissociation of slag iron, tailings metal iron content ≤ 1%, energy consumption is 30% lower than traditional equipment.
Advantages of steel slag crushing programme
Through three-stage crushing + four magnetic separation (suspended magnetic, cylinder magnetic separator, etc.), large slag steel (TFe>80%), particle steel (TFe 60-85%), fine powder (TFe 30-60%) can be recovered. The metal iron content of tailing slag is ≤1%, which meets the standard of building material aggregate (e.g. concrete aggregate needs to be ≤5mm).
Energy saving and environmental protection
Adopt ‘more crushing and less grinding’ process to reduce the energy consumption of grinding (steel slag Bond Index 20-30kW-h/t). Equipped with pulse dust collector (dust concentration ≤20mg/m³) and soundproof cover, in line with environmental emission standards.